山東滬工閥門制造股份有限公司
銷售電話:15963678999
技術(shù)電話:18663605695
售后電話:18753688979
投訴電話:13805368625
傳真號碼:0536-8327588
郵箱:sdhgfm@163.com
地址:山東濰坊經(jīng)濟開發(fā)區(qū)泰祥街與文化路中南高科鳶都匯智產(chǎn)業(yè)園91
現(xiàn)代煤化工對閥門的技術(shù)要求
點擊次數(shù):836更新時間:2020-04-10

一、閥門材料要求
直接液化也叫加氫液化。在加氫過程中,其閥門、管道及相關(guān)設(shè)備處于高溫高壓氫氣中,氫損傷就是一個很大的問題。高溫高壓硫化氫與氫共存時的腐蝕也很嚴重。正因為如此,為抗高溫硫化氫的腐蝕通常閥門材料會選用奧氏體不銹鋼。這樣又有可能出現(xiàn)不銹鋼的氫脆、奧氏體不銹鋼的硫化物應(yīng)力腐蝕開裂及堆焊層氫致剝離現(xiàn)象等損傷。另外還有Cr-Mo 鋼的回火脆性破壞的問題。而且,物流中存在的氨和硫化氫等腐蝕介質(zhì)可能引起的損傷等也是必須加以慎重考慮的。由于煤直接液化反應(yīng)中有油煤漿的存在,煤漿對閥門、管道等設(shè)備材料的磨損問題必須要進行考慮。因此要求用于制造閥門的材料要具有符合使用要求的綜合性能。具體來說,應(yīng)該具有:
( 1) 作為描述材料內(nèi)質(zhì)特性的致密性、純潔性和均質(zhì)性性能要優(yōu)越,這對于厚( 或大斷面) 鋼材尤為重要。
( 2) 要具備滿足設(shè)計規(guī)范要求的化學(xué)成分、室溫和高溫力學(xué)性能的要求。
( 3) 要具有能夠在苛刻環(huán)境下長期使用的抗環(huán)境脆化性能。
在閥門招標文件中對于閥門的致密度有明確的要求,對于鍛造閥門,一般會通過對鍛件的鍛造比、晶粒度等要求,來實現(xiàn)控制致密度的要求。但是,對于鑄造閥門,只是在相關(guān)的技術(shù)文件中,提到應(yīng)使鑄件體致密度均勻,消除鑄件的縮孔與縮松,少有見到量化指標。其實恰恰是鑄造閥門,往往因為對鑄造工藝的質(zhì)量控制不同,造成閥門鑄件的質(zhì)量差別很大,主要影響因素有:成型材料的選擇不同,澆冒口的設(shè)置不同,冷鐵位置與數(shù)量的選擇不同,凝固順序的差異,以及冷卻時間的不同等,都會導(dǎo)致其致密度、均質(zhì)性性能差別很大。后續(xù)的熱處理工藝也是閥門質(zhì)量保證的非常關(guān)鍵的步驟之一,熱處理爐的溫控、鑄件在熱處理爐中的碼放、保溫時間及冷卻方式與速度等因素都會影響*終閥門鑄件的機械性能。
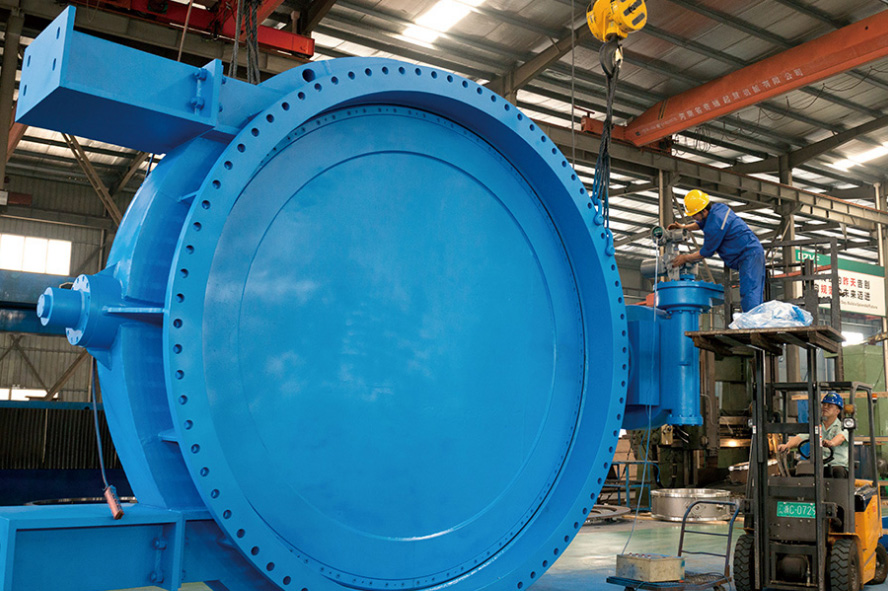
二、閥門工藝要求
煤直接液化既有加氫裝置高溫、高壓、臨氫的特性,又有煤化工腐蝕磨損工況并存的特點,因此,原材料的來源非常關(guān)鍵,目前,還沒有找到一個行之有效的方法來控制原材料的選用,一般來講,對閥門材質(zhì)的成分尤其是有害元素含量,如S、P、O、N 及總碳當量等,提出相應(yīng)的明確的指標要求,雖然這種要求往往高于材料的基本普通要求,但是,對于*終產(chǎn)品質(zhì)量,僅靠這些成分指標還是不夠的,因為影響原材料機械性能的微量元素遠不止這些。嚴格的講,我們的要求僅是對常見的危害材料機械性能的微量元素予以控制,并沒有也不可能完全將所有可能出現(xiàn)的對金屬材料機械性能有害元素成分全部羅列出來。因此,鑄造廠應(yīng)該嚴格控制原料來源,對于所加工的原料不僅應(yīng)該進行熔煉,還應(yīng)該進一步進行精煉,特別是加強爐前控制,只有這樣才有可能保證鑄件質(zhì)量。
在保證原材料質(zhì)量的前提下,針對該類裝置還有一些特殊的要求:
(1) 對于現(xiàn)代煤化工裝置的鑄造閥門不能采用精密鑄造工藝。因為煤液化即是加氫裂化工藝,由于氫分子對金屬材料特殊的穿透性,而精密鑄造出來的鑄件比較疏松,均勻性也較差,因此,對于臨氫工況和高溫高壓工況都不適宜采用精密鑄造工藝取得閥門鑄件;
(2) 奧氏體不銹鋼要進行固溶化熱處理( 固溶化熱處理溫度為1050 ± 10℃) ,對于321 和347材料,還應(yīng)進行穩(wěn)定化熱處理( 穩(wěn)定化溫度為900± 10℃);
(3) 熱處理爐不應(yīng)采用燃煤加熱爐,應(yīng)采用電加熱爐或者是天然氣加熱爐,鑄件在加熱爐內(nèi)碼放應(yīng)利于爐內(nèi)氣流循環(huán)。由于煤加熱爐會加大爐體各部位的溫差,因此,不能采用燃煤加熱爐;
(4) 鑄件試棒的選取應(yīng)為聯(lián)體試件。“分體”試棒無論是澆鑄過程還是熱處理過程都無法真正代表鑄件本身的特性,與鑄件本身實際的機械性能存在較大的誤差,因此,不能采用“分體”試棒檢驗;
(5) 所有閥門必須對鑄件進行射線檢查,檢查的范圍包括閥體、密封元件、閥蓋,鑄鋼件在凝固過程中易產(chǎn)生缺陷,尤其對于鑄鋼件的關(guān)鍵部位、應(yīng)力集中區(qū)域、承壓能力薄弱的部位等,應(yīng)特別加以關(guān)注。對于碳鋼、合金鋼鑄造閥門,應(yīng)逐件進行磁粉或液體滲透檢查。檢查范圍: 閥體、閥蓋和密封元件的外表面及可觸及的內(nèi)表面和閥桿。對于不銹鋼鑄造閥門,應(yīng)逐件進行液體滲透檢查。檢查范圍: 閥體、閥蓋和密封件的外表面及可觸及的內(nèi)表面和閥桿;
(6) 每個承壓鑄件的所有補焊面積總和應(yīng)不超過鑄件的表面積的10%;每個承壓鑄件的重大補焊數(shù)量,DN50~DN100 不超過1個;DN150 ~DN250 不超過2 個;DN300 ~DN350 不超過3 個。
上述鑄造缺陷的補焊應(yīng)在*終熱處理之前進行;當在射線探傷時發(fā)現(xiàn)有缺陷,且屬于可補焊修復(fù)的,允許進行1 次補焊。補焊后應(yīng)重新拍片檢驗,檢驗合格后該鑄件必須重新進行熱處理。補焊應(yīng)具備焊接規(guī)程及工藝鑒定證書,填充金屬的物理、化學(xué)性能及耐腐蝕性均應(yīng)與母體金屬接近。所有受壓組件的缺陷*終熱處理之后,均不允許通過焊補進行修理。
要具有能夠在苛刻環(huán)境下長期使用的抗環(huán)境脆化性能
對于操作在高溫高壓氫環(huán)境下的閥門,在操作狀態(tài)下,閥門內(nèi)壁中會吸收一定量的氫。在停工的過程中,若冷卻速度太快,使吸附的氫來不及擴散出來,造成過飽和氫殘留在器壁內(nèi),就可能在溫度低于150℃時引起亞臨界裂紋擴展,給閥門的安全使用帶來威脅。閥門制造廠在閥門焊接時需要注意控制TP347 中δ 鐵素體含量,焊態(tài)時*大值以10%為宜( 為防止焊接中產(chǎn)生熱裂紋,下限可控制不低于3% ) ,以避免含量過多時在焊后*終熱處理過程發(fā)生較多的相變,而產(chǎn)生脆性。
三、閥門結(jié)構(gòu)要求
閥門結(jié)構(gòu)的設(shè)計應(yīng)避免煤漿結(jié)焦使閥門失效并方便清洗。油煤漿有一個特點:如果流通不暢或者靜止不動,也就是介質(zhì)的流況不好,將會沉積并有可能發(fā)生聚合反應(yīng),從而出現(xiàn)結(jié)焦并使閥門抱死。目前在直接液化煤漿管道上使用的切斷閥門全部是球閥,當操作需要切斷管道將球閥關(guān)閉時,閥球內(nèi)部的油煤漿因為無法排出,沉積在球腔內(nèi),就有可能結(jié)焦抱死。當球閥關(guān)閉后,煤漿因為沉積結(jié)焦而致閥球無法再次打并將球閥的耐磨層毀損剝落。所以,其實在此工況下選用球閥并不是*合適的選擇。
四、閥門耐磨要求
漿料工況下使用的球閥應(yīng)采用金屬硬密封形式,且閥座與球的材質(zhì)相同,確保兩者有相同的膨脹系數(shù),在高溫的條件下不會出現(xiàn)球體‘卡死’的現(xiàn)象。由于閥門的很多使用工況是在高溫高壓下的,根據(jù)使用經(jīng)驗,有些閥門在常溫下測試沒有問題,但是在高溫工況下發(fā)生啟閉操作困難,究其原因是閥芯與閥體之間產(chǎn)生不同步熱脹造成的。所以,生產(chǎn)廠在出廠前應(yīng)做高溫啟閉試驗。但高溫啟閉試驗絕不是將整個閥門投入熱源中,使閥門整個溫度升高,這樣所得到的測試結(jié)果與實際情況是不符合的。因為,在真正使用過程中,閥門是因介質(zhì)溫度高而升溫的,此時是閥芯先熱而閥體外表面隨后慢熱起來,如果將整個閥門投入熱源中,則閥體先熱而閥芯后熱,與實際工況正好相反,起不到測試的目的。高溫啟閉試驗應(yīng)建立與實踐工況相一致的溫度梯度。
涂層與基本材質(zhì)的膨脹率應(yīng)相近。否則,在高溫和常溫交變過程或者高溫下,易產(chǎn)生龜裂,從而更易使涂層剝落。對超音速噴涂(HVOF) 或類似的方法,涂層表面硬度為64~68HRC,結(jié)合強度不小于10MPa;對冶金熔合或類似的方法,涂層表面硬度為62 ~68HRC,結(jié)合強度不小于70 MPa。涂層的有效厚度(不包括過渡層) 為0.2 ~0.5mm。閥座應(yīng)采用刮刀式設(shè)計。在球體轉(zhuǎn)動時可提供一個掛刷的動作,防止閥球與閥座間的顆粒沉積。在設(shè)計時,應(yīng)該注意,利用刮刀可以將球體與閥座間的顆粒掛刷掉,但是,這種刮刀設(shè)計在有的工況下會帶來另一個問題: 因為附帶了刮刀設(shè)計,在刮刀處形成了一個銳角,而這種銳角勢必產(chǎn)生應(yīng)力集中現(xiàn)象,更加不利于涂層與基材之間的結(jié)合,在磨蝕工況下,更易導(dǎo)致涂層的剝落,致使閥座毀損。
?